"Initially, our studio was (started from) creating various things using 3D printers."
3D printers have rapidly become widespread all over the world since 2014, when the basic technology sprouted in the 1980s and the patent protection period for key technologies ended after the continuous development of related technologies. In the midst of the boom that arrived in Taiwan from 2014 to 2016, Mr. Tseng and his colleagues participated in various projects while learning about 3D printing materials and its applied technologies. With rapid prototyping, which produces only shapes at an early stage in the process of product development, they became proficient in achieving quick delivery with a quality that surpassed their competitors. Under these circumstances, they were initially involved in the development of the 3D printer itself, they gradually shifted their focus to its utilization.
At STUDIO KAGE SAMURAI, they handle 1) graphic design, 2) web design, 3) interior design, 4) product development and design, 5) 3C (general term for computers, communications and home appliances often used in Taiwan) 6) planning and support for various events. Among these, the 3D printing application work the company handles are 1) support for the production of three-dimensional objects of design deliverables to university students such as graduation works, 2) production of prototypes of industrial design, 3) production of souvenirs designed by other companies or in-house, and so on. There, they make full use of their know-how gained through the development experience of 3D printers, especially in the detailed processing in the finishing process such as coating and coloring, or in selecting the optimum material that differs for each product or work. Mr. Tseng positions that the company's strength is being able to create three-dimensional objects faster and more beautifully while ensuring the quality required for the project.
They introduced Shade3D in 2014, a year before the establishment of the company. While interacting and exchanging information with friends, there was a high-precision model that he was interested in, and he found Shade3D while exploring what kind of software it was made with. First, they got the model file created in Shade3D through the website. They printed it in 3D and realized the high degree of perfection. Next, when they tried the trial version of Shade3D, they found it easy to operate and use even for beginners, so they officially decided to purchase it.
In particular, Mr. Tseng noted that Shade3D has a file repair function that supports 3D printing and can output model files with better quality. In addition, he points out the advantages of supporting various file formats such as STL, IGES, 3ds, and OBJ.
As recent examples of working with Shade3D, he lists out 1) a sword object that has been designed in-house and has been carefully modified in detail, and 2) a powerful painting booth that removes excess paint when coloring models, 3) spare keys for servers, etc. Each of them will be marketed as in-house products or OEM products in the near future.
Having used the product themselves, they are convinced of the potential of Shade3D as 3DCG software. Mr. Tseng has cultivated the desire to spread the use of the software not only to STUDIO KAGE SAMURAI's business partners but also to people in other industries. In embodying this, Shade3D is positioned as part of the sales of digital (3C) products, which is one of the pillars of the company's business as previously mentioned. They are considering commercializing the agency sales in the Taiwan market.
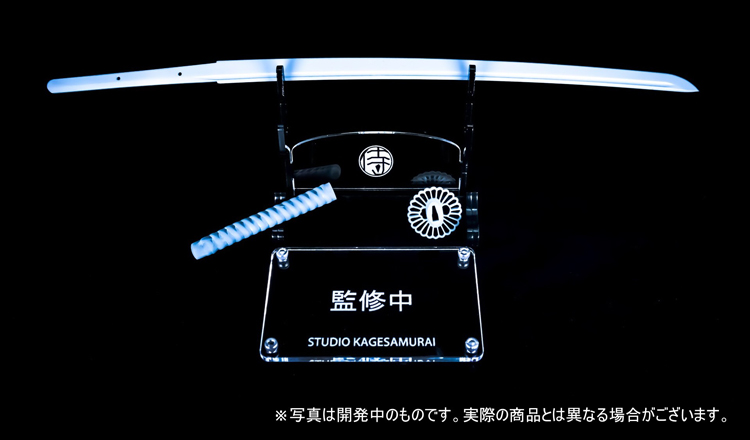 |
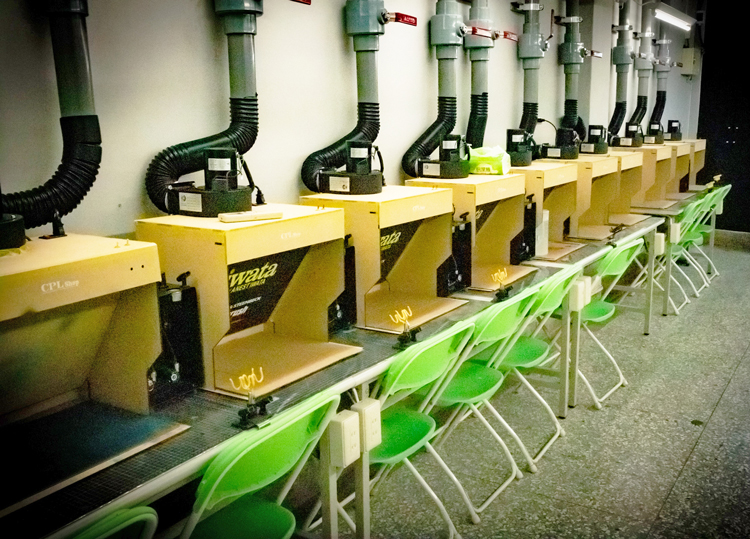 |
▲1/3 sword model |
▲Painting booth for models (small) |
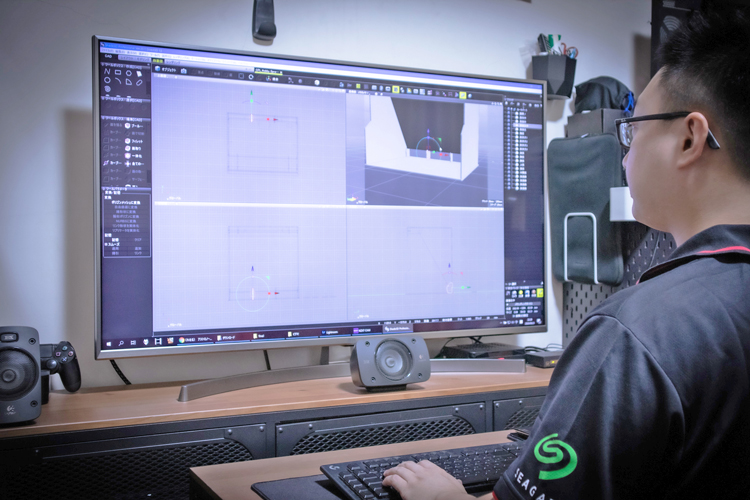 |
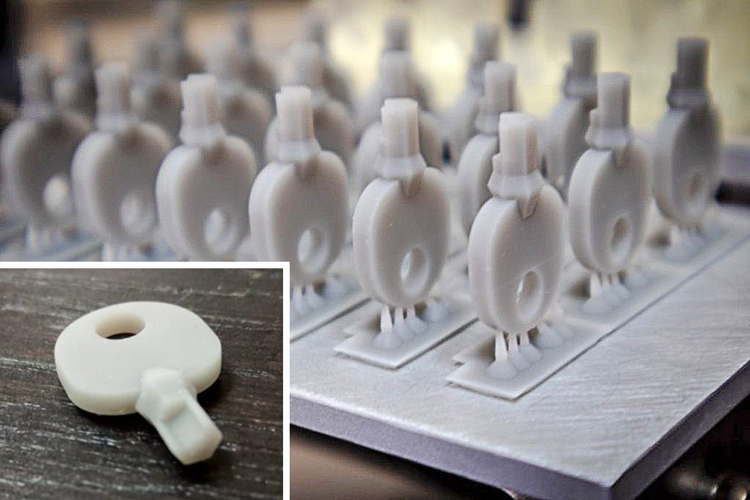 |
▲CPL strong painting booth for models (large) |
▲Spare keys for servers |
|